ABOUT
US
PRODUCTS
COPPER
COPPER IS DUCTILE
Compared to other metals, copper is very ductile, meaning that it can be drawn through a tiny hole into very fine wire without breaking. Refining improves the ductility of copper so that extremely fine wires can be drawn. Impurities increase the chance that the wire will break during the drawing process.
Copper conducts electricity.
Only silver conducts electricity better than copper and traditionally costs 40 times the price of copper. Refining improves the conductivity of copper by lowering the electrical resistance. Resistance is like friction to electricity, and it causes energy to be lost as heat in poorly conducting wires. Improved conductivity means more energy is delivered to the desired destination when you flip that switch or turn that dial.
COPPER IS RECYCLABLE
More than one-third of the copper refined in the United States comes from recycled material. That’s a higher recycling rate than aluminum! Scrap copper comes from manufacturers of all sorts of copper and brass products. The copper is melted and cast into anodes and refined just like “new” copper from the mines and smelters.
ASARCO' S COPPER BUSINESS
RESOURCES
COPPER PRODUCTS SPECS
MAKING COPPER
ASARCO' S COPPER BUSINESS
ASARCO OFFERS REFINED COPPER IN A WIDE
VARIETY OF SHAPES AND SIZES
Amarillo Copper Refinery’ s Management/Quality Systems is ISO 9001:2000 certified.
Copper production is monitored and controlled, assuring compliance with the world’ s highest production standards.
Systems are calibrated, controlled, and documented to affirm top quality performance and products.
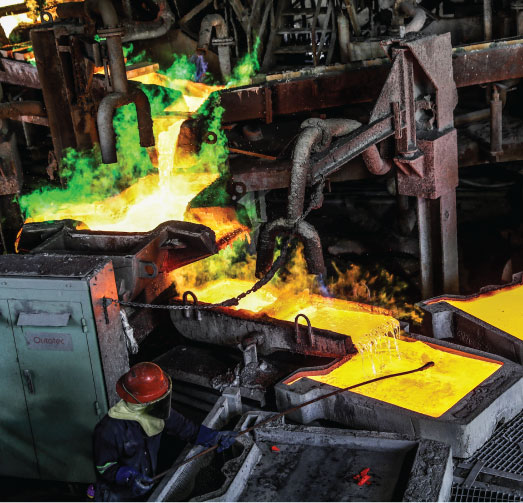
RESOURCES
ASARCO: A RELIABLE SOURCE FOR REFINED COPPER
One of the key factors in maintaining a reliable supply of product is close control over the flow of materials during the production process.
ASARCOÂ maintains this control through its integration of operations and by applying quality control production standards.
MINES
ASARCO’ s Ray Unit has the capacity to produce approximately 100 million pounds per year of electrowon copper cathodes from its SX/EW plant. The Company’ s Silver Bell Unit produces about 40 million pounds of SX/EW cathodes annually.

EXPLORATION
To maintain its reliability as a supplier, ASARCOÂ conducts an ongoing exploration program for new copper-bearing mineral deposits and continuously drills at existing deposits to expand and delineate the ore body.
HOW TO SPECIFY COPPER SHAPES:
ASARCO’ s electrolytic copper shapes are made to conform to the specifications of the American Society for Testing and Materials (ASTM). The applicable
permissible variations specified by ASTM are listed in the tables showing dimensions and weights for the various refinery shapes.
COPPER PRODUCTS SPECS
The high-quality, electrolytic tough pitch (ETP) copper cathode and rod produced by ASARCO meets or exceeds the chemical analysis specified by the American Society for Testing and Materials (ASTM).
So, too, does the Company’ s ETP copper cake.
+ Â Â ROD
CONTINOUS-CAST ROD SPECIFICATIONS
ATR BRAND, ELECTROLYTIC TOUGH
PITCH (ETP) PICKLED AND COATED
Continuously cast copper rod produced at our Amarillo Copper Refinery is
shipped to wire manufacturers all over North America.
MAKING COPPER
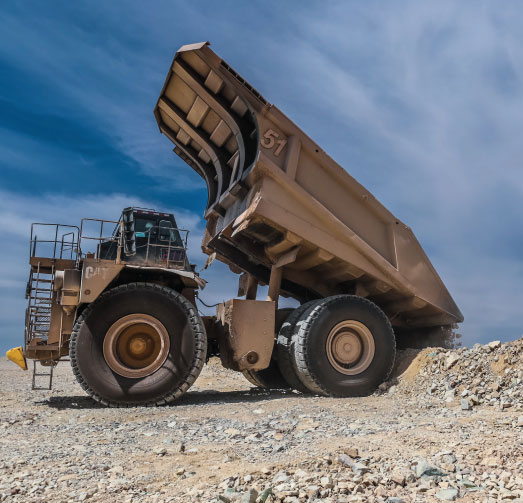
MINING
Arizona is nicknamed “The Copper State” because of the great deposits of copper that NATURE has placed here. If Arizona was a country, it would be the second largest producer of copper in the entire world. Only Chile produces more copper than Arizona. The star on the Arizona state flag is copper-colored because the red metal is so important to the state’ s economy.
A miner is even depicted on the state seal. ASARCO currently operates three copper mine properties in Arizona:
+ The Ray Complex mine and mill, between Hayden and Superior, Arizona
+ The Silver Bell mine and SX/EW plant, northwest of Tucson, Arizona
+ The Mission Complex mine and mill, south of Tucson
MINING RESOURCES
+ Drilling and Blasting Crew
+ Big Trucks and Big Shovels
+ Truck Dispatch System
+ Dust Control
MILLING
CRUSHING
The haul trucks carry the ore out of the pit along a haulage road with a slope of no more than about nine percent. They dump the ore into a gyratory crusher which reduces the ore to eight inches or less — about the size of soccer balls. The primary crusher may send the crushed ore on to a secondary crusher or pile it directly onto the coarse ore stockpile.
On your tour from the Mineral Discovery Center, you may get to see the haul trucks dumping ore into the crusher
GRINDING
The ore is ground into a fine powder by large rotating mills. The two types used in the Mission South Mill are called SAG (semi-autogenous grinding) mills and ball mills.
SAG mills use larger pieces of ore to break up the smaller pieces (autogenous—does it by itself). The larger pieces also break down. To help the process along, eight-inch-diameter steel balls are added to the rocks as they tumble inside the rotating mill (semi-autogenous—gets some help from the steel balls).
When the rocks are about 3/8-inch or smaller, they are fed as a slurry into the two ball mills. These mills contain literally hundreds of thousands of three-inch diameter steel balls that pulverize the ore until it is like fine sand or face powder. Only then are the copper minerals broken free of the rest of the rock to be separated by flotation
CONCENTRATING
The slurry of water and pulverized ore is mixed with milk of lime to raise the pH and small amounts of special reagents: a frother to make bubbles, and a collector chemical that causes the copper minerals to stick to those bubbles.
Air is blown into the tank and the mixture is vigorously agitated like a high-speed blender. Rising bubbles carry the copper minerals up and over the edge of the flotation tank. The bubbles break soon after they flow over the edge. The copper minerals are then ground up even finer and purified by another flotation process.
The dried copper concentrate of about 28 percent copper is shipped to the smelter. It represents less than one percent of the material removed from the mine. Concentrate is just a fine powder of the mineral chalcopyrite which is a naturally occurring compound of copper, iron, and sulfur.
The material that sinks in the first flotation cell goes on to two more flotation cells to recover as much copper as possible. What doesn’t float is called tailings because it goes out the “tail end” of the flotation circuit.
About 80 percent of the water used in the milling process is reclaimed and re-used. The rest is used to keep the tailings damp and to prevent wind-blown dust.
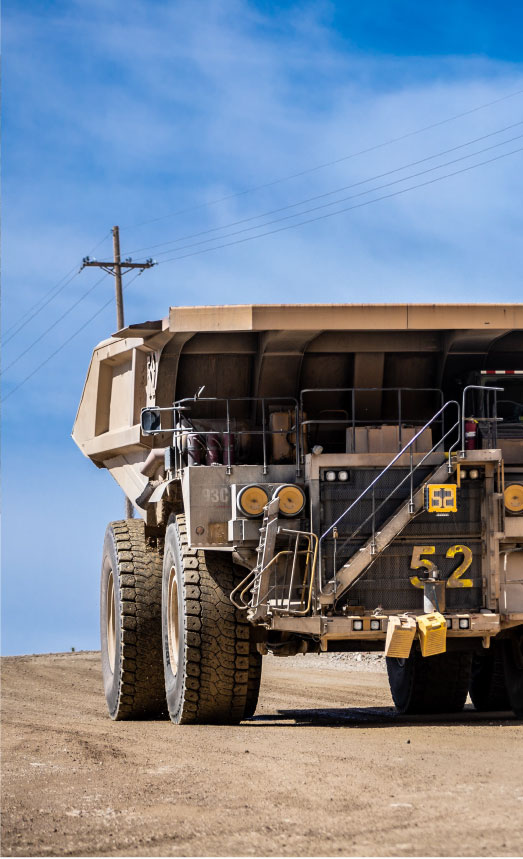